Plasma Thermal spray systems
The plasma spray process is commonly referred to as air or atmospheric plasma spray (APS). The plasma spray process involves the latent heat of ionized gas (plasma) as a heat source. The most common plasma gas combination is Argon/Hydrogen. Other gases used are typically Nitrogen and Helium.
Plasma spray coating process
In this process, the heat source (plasma) is formed by the generation of a high-density arc current in the space between a cathode and an anode filled with a monatomic gas such as argon and a diatomic gas such as hydrogen. The ionized gases heat up to temperatures approaching 15,000°C and expand to reach supersonic gas exit velocities.
Properties of the plasma stream can be controlled by cathode-nozzle configuration, gas type, gas flow, gas mixture ratio and electric arc power levels. The resulting plasma stream can therefore greatly influence the degree of melting and acceleration of the chosen material, allowing deposition of coatings with tailored microstructural properties for specific industrial applications.
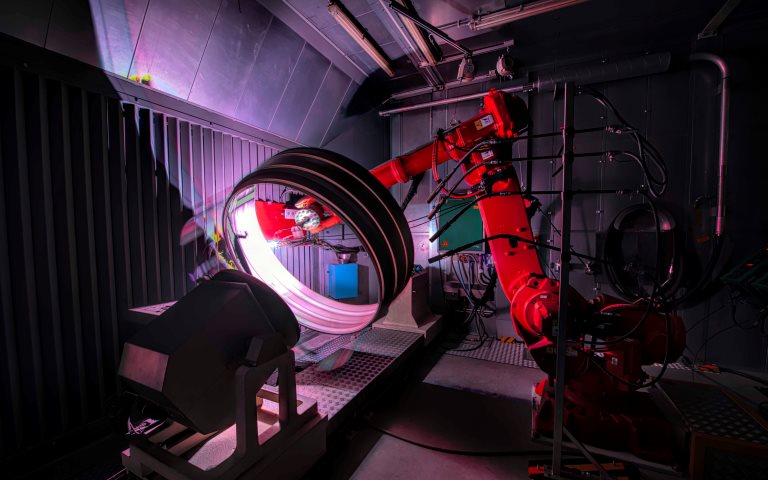
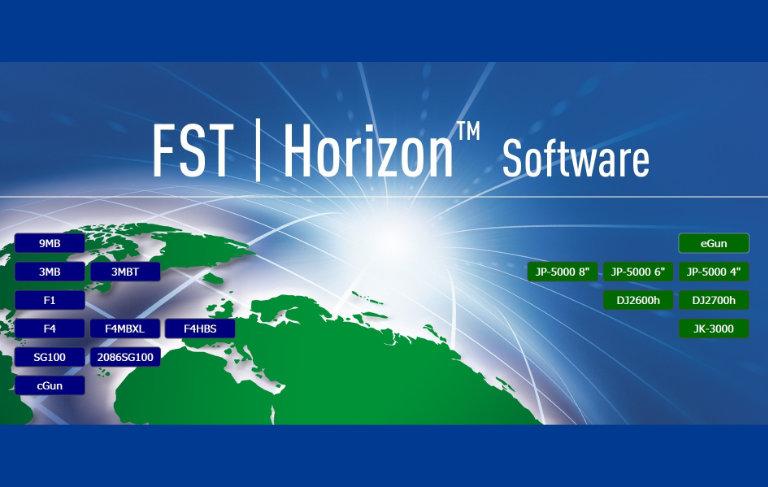
HorizonTM software
FST Horizon™ professional Thermal Spray Software – operates multiple thermal spray processes in one modular software platform. Increase your production output by using FST’s reliable, versatile, unmatched process control delivered by FST’s 50 Digital Series systems.
More information about Plasma process?
Atmospheric Plasma Spray (APS) is the most versatile and flexible thermal spray process due to its ability to spray a wide range of materials such as most metals, ceramics and alloys onto many different substrate materials such as plastics, glass, metals, ceramics and composite materials. Also, a broad range of powder particle sizes can be used. Benefits of APS applied coatings include resistance against oxidation, wear from abrasion and erosion, corrosion protection, clearance control, temperature management as well as electrical resistivity and conductivity. Thus APS coatings can be used for a wide range of applications across industries.