Turn-Key Systems
FST designs, manufactures and has installed turn-key systems & projects all over the world for different industries and applications. Turn-key coating systems are fully engineered and integrated facilities, designed to offer tailor-made and best practice solutions. Typically, a system includes the core coating and control equipment, and all required peripheral components, such as sound-proof spray booths, robotic handling, turntables, dust collectors. These components are fully integrated for operation in automatic mode. This also allows the user to monitor and control the operational status, and all alarm and e-stop features.
Turn-key project overview
Project Management
Engineering & design
Technical kick-off meeting
Thermal spray equipment manufacturing
Factory acceptance testing (FAT)
Site acceptance testing (SAT)
Know-how transfer / Qualification
Installation
Training
Maintenance / Service / Support
Thermal Spray Processes
FST offers the full range of Thermal Spray process equipment. Besides stand-alone units for plasma, HVOF, powder/wire Flame, or electric arc spraying, also Multi-Process Systems can be provided, such as our sophisticated MP-50 Digital Series. This modular system can handle several processes with only one controller. The PLC-based MP-50 also controls the functions of all peripheral systems. Because of the extended experience and expertise available within FST, especially in the field of coating applications and related production and product requirements, a transfer of technology and know-how can also be offered as part of the Turn-key Project.
Service & Support
After installation, FST can offer the customer specific application know-how, parameter and component development, process optimisation, robot programming, and many more services. This enables the customer to start with his production soon after final acceptance, without having to go through the “learning-curve”. The main key to the successful realisation of our Turn-key Projects is the fact that FST has proven to be an experienced, reliable, and knowledgeable partner for Turn-key Systems, Thermal Spray equipment, Materials and Service.
Safety & Quality
FST is committed to implementing the highest safety and quality during designing, manufacturing and installation of our systems. Only first-class components are used, while the smart system and software design together with integrated sensors and e-stops assure the safest possible operation. The system layout and customer set-up is engineered to reach the most efficient operation and effective production. After installation of the equipment, dedicated training is provided on system operation, maintenance and Thermal Spray technology, as a natural part of the entire project.
Auxiliary Equipment
FST references
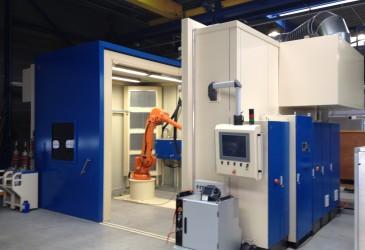
Project TEI 1.0
Robotic Thermal Spray System
MP-X/APS/HVOF
Application/Industry:
Aerospace
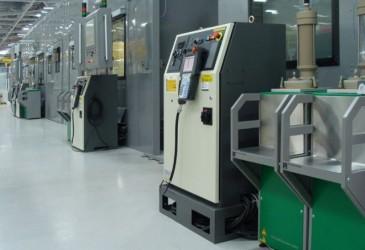
Project Siemens WS
5x Robotic Thermal Spray System
MP-X/APS/HVOF
Application/Industry:
Industrial Gas Turbine
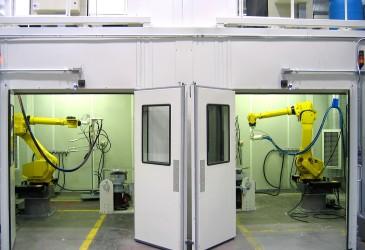
Project Siemens TX
2x Robotic Thermal Spray Systems
MP-X/APS/HVOF
Application/Industry:
Industrial Gas Turbine
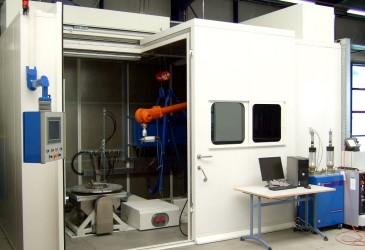
Project Wamar
Robotic Thermal Spray System
MP-X/APS/HVOF
Application/Industry:
Industrial Gas Turbine
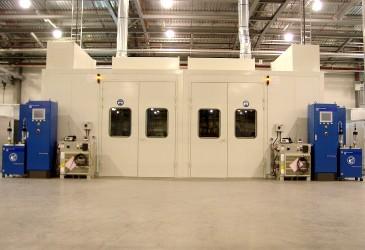
Project Rolls Royce
2x Robotic Thermal Spray System
MP-X/APS/HVOF
Application/Industry:
Aerospace
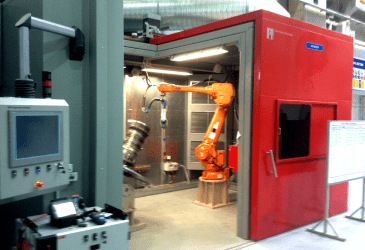
Project Maintenance Partners
Robotic Thermal Spray System
MP-X/APS/HVOF
Application/Industry:
Industrial Gas Turbine
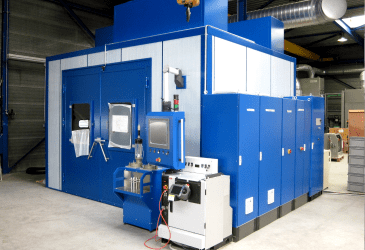
Project MJB
Robotic Thermal Spray System
MP-X/APS/HVOF
Application/Industry:
Industrial Gas Turbine
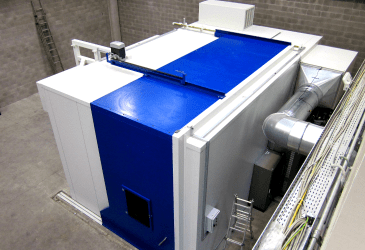
Project Cromostamp
Turn-key Thermal Spray System
MP-50/APS/HVOF
Application/Industry:
General Engineering
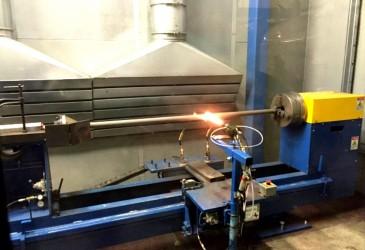
Project Coastal Hydraulics
Turnkey Thermal Spray System
eGun™ System Mobile
Application/Industry:
Hydraulics
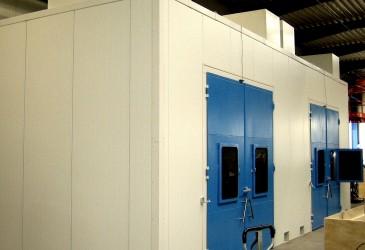
Project RRBS
4x Thermal Spray Systems
Application/Industry:
General Engineering
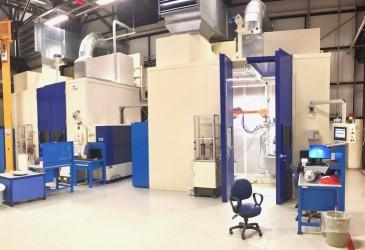
Project TEI 2.0
2x Robotic Thermal Spray Systems
MP-50 APS/HVOF
Application/Industry:
Aerospace
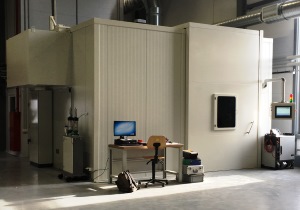
Project Siemens
Robotic Thermal Spray System
MP-50 APS/HVOF
Application/Industry:
Industrial Gas Turbine
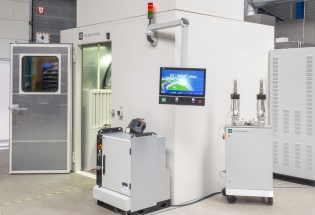
Project Sartori
1x Robotic Thermal Spray System
AP-50 APS
Application/Industry:
Medical Implants
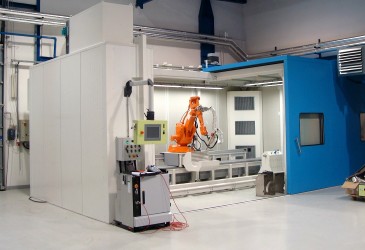
Project Safina
1x Robotic Thermal Spray System
Cold gas system turn-key
Application/Industry:
Precious metals
Turn-key System Concept Coating Facility
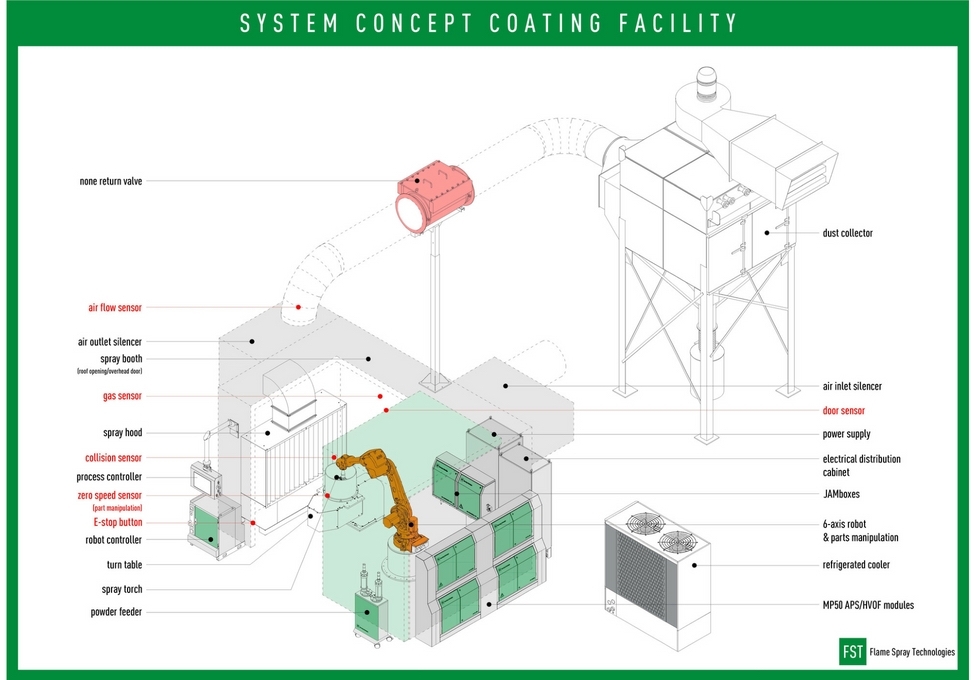
Non-return valve: the purpose of the ATEX non-return valve is to prevent a deflagration (explosion) that could occur in the dust collector from travelling back down the inlet pipe back into the spray booth.
Airflow sensor: this safety feature assures the dust extraction flow is active during the process. Without flow, the process cannot be started or shut down safely.
Air outlet silencer: with process noise up to 135dB, this outlet silencer reduces the noise outside the spray booth to acceptable levels. Each silencer is designed for optimal flow throughout.
Spray booth: Typical thermal spray installations include an enclosure that protects the operator and the surrounding areas from the hazards associated with the thermal spray process while it is in operation. The structure of a typical thermal spray booth has the primary function of controlling exposure to the following major hazards:
- Excessive sound levels
- Powder/dust from the process
- Gases/Fumes
- Visible light and ultraviolet (U.V.) radiation
The configuration of a typical thermal spray booth centers on an enclosure structure that works with other sub-systems (interlocks, controls, ventilation/filtration) to provide effective control and protection from these major hazards. Each thermal spray booth FST provides is design to be optimally effective for your specific spray operations.
Gas sensor: used to block gas flows under certain conditions in addition to problems with lack of ventilation.
Collision sensor: robotic Collision Sensors mechanically detect when the robot arm has encountered an obstruction, absorb the crash energy and quickly stop the robot to prevent costly damage to the robot arm, spray object and spray torch.
Process controller: FST’s Horizon operating software is controlled from this 22’’ human machine interface touch screen. The HMI can be wall mounted or on a tool post, both adjustable to optimal ergonomic positions.
Zero speed sensor: in case no rotation of the turntable or spray lathe is detected while this is part of the program, the spray process will automatically shut down. This prevents parts from being damaged and potentially hazardous situations.
E-stop: typically push to lock – pull to release button(s) provided to remove power (as appropriate) in an emergency. All E-stop buttons in a spray system perform the same function. The E-stop(s) are positioned to be easily accessible its function is intended for use in Emergency conditions to try to limit or avert harm to someone or something. Activating one of the E-stops immediately causes a complete stop for both thermal spray process and robotic movements.
Robot controller: control centrum of the robot handling equipment.
Turntable: combined and integrated or stand-alone controlled component manipulation system, specially designed for automatic and reproducible coating applications for the specified components.
Spray torch: multiple torch technology; handles most plasma/HVOF spray torches, including for plasma: cGun, F4, F100, 3/7/9MB (MBT), SG-100, I.D. torches and for HVOF: eGun, JP-5000 and diamond jet and most other available HVOF process torches.
Powder feeder: the powder feeder that can be used with all powder based thermal spray processes including plasma and HVOF. The powder feeder can be foreseen with different options such as weight loss option and heater blankets.
Dust collector: the use of air flow in the thermal spray process is required to meet worldwide operator safety and environmental regulations. The reasons for having an exhaust system are as follows:
- Provide adequate airflow through the booth to prevent the buildup of combustible or explosive gases in the enclosed area to allow safe operation of the thermal spray process.
- Proper air flow removes gases, fumes, reaction by-products (metal compounds and gases), and dust particles from the air inside the spray booth, and prevents inhalation by personnel working in the area, and filtration prevents contamination of the environment.
- Thermal spray processes use gases to convey the coating materials to the flame, plasma or arc. During the coating process, the effluents from the coating process that are not consumed by the process, or deposited on the part, must be removed from the spray environment to protect the equipment and prevent operator exposure to hazards.
- Thermal spray processes produce heat, which if not removed will slowly elevate the booth temperature to unsafe levels.
- Improper ventilation can have detrimental effects on coating quality.
Source: Thermal Spray Booth Design Guidelines, Prepared by the ASM-TSS Safety Committee.
Door sensor/door interlock: access door interlocks – switches that require doors to be fully closed to enable process start, and stop the process if opened during operation.
Power supply: in case of the APS thermal spray process, a power supply unit will be provided for the operation of different plasma torches at a high and constant quality level.
Electrical distribution cabinet: FST’s turn-key solutions are provided with a single cabinet that houses all electrical connections for each turn-key system subcomponent. The EDC also contains all circuit breakers. Also has a main switch is incorporated into the EDC. With this distribution cabinet, only one main connection of the electricity supply from the customer is required.
Jamboxes: For each process, a jambox cabinet is usually mounted inside the spray booth. Gasses and power for the APS process (AP-50) are distributed to this jambox. Liquid or gas fuels are distributed for the HVOF process (HV-50). The spray torch hoses and cables set is connected to the jambox. In case of multi-process (MP-50), a water switch module is built into the HV-50 jambox. The AP-50 Jambox also contains a high voltage discharge unit for APS torch ignition and a water flow meter for safeguarding water flow for spray torch cooling.
Robot & part manipulation: each FST system is developed and designed taking into account the shape, weight and quantity of the foreseen to be sprayed components. FST offers a wide variety of components handling systems. Heavy or lightweight, high or low quantities, large or small components, high precision, high-speed FST will design each system to be of optimal usage for your application. All equipment of the turn-key system is integrated to a level that fits the application requirements. In most cases, the robotic equipment master-slave controls all other components of the total turn-key solution. This set-up assures for optimal process control which increases the coating quality consistency.
Refrigerated cooler: all high-end thermal spray processes require water cooling to maintain spray torch stability and effectiveness. In case of the APS process, a deionizer is built into the water chiller to minimise corrosion in the gun and control conductivity. Water temperature in the plasma and HVOF spray torch has a direct effect on the coating and therefore should be kept at a constant temperature, above the dew point. FST’s refrigerated coolers closed loop control the water temperature within a few degrees.
50 Digital Series: the 50 digital series system is a closed loop controlled thermal spray system using state of the art Mass Flow Controllers for process gasses and carrier gasses. The system is foreseen with various safety features and closed loop control of all important process components. The control system is based on Siemens 1500PLC technology. Remote Diagnostics, data reporting, turn-key maintenance scheduler are features of the FST Horizon software. The MP-50 is designed around modularity by working with separate gas Modules and jamboxes for each of the processes. Together with the control system, this significantly enhances the safety, stability and reliability of the entire system. The Touch Screen interface (with Horizon operation software in English or in other languages at request) follows a logical set-up and is operator friendly and easy to use.
The Coating Machine™
The Coating Machine™ is a very complete - plug and play - flame spray production unit designed to service a wide variety of markets. The autonomously operating units are engineered with standardization in mind, whilst providing customers multiple options to accommodate their specific needs.
The Coating Machine™ is available in three different configurations and is fully compatible with all conventional coating processes including: APS, HVOF, Flame Wire, Flame Powder and Arc-Spray. Typically, the system will be operated using FTS’s state of the art Digital 50 Series process controllers.
The three available configurations of The Coating Machine:
1. The Coating Machine™ Type I
- ABB IRB 4600 45/2.05 Robot, T1200 Non-Tilting Turn Table (1,200kg max. load)
- ABB IRB 4600 45/2.05 Robot, LTT1200 Tilting Turn Table (1,200kg max. load)
![]() |
![]() |
2. The Coating Machine™ Type II
- ABB IRB 4600 45/2.05, 2 Station Carousel (100kg max. load)
- ABB IRB 4600 45/2.05, 8 Station Carousel (25kg max. load)
![]() |
![]() |
3. The Coating Machine™ Type III
- ABB IRB 4600 40/2.55, L3500 Spray Lathe, 2,500mm between centres (1,000kg max. load)
- ABB IRB 4600 40/2.55, L2500 Spray Lathe & Turn Table (Lathe: 1,000kg and Turntable 300 kg max. load)
![]() |
![]() |
The Coating Machine provides the following benefits:
Cost reduction due to standardization, with options to choose from
Pre-installed and commissioned equipment
Shipped as a fully operational unit, production ready
Essentially plug and play spray facility
Robustly built to the highest standard